Top Benefits of Using Remote Controlled Electric Auger Dredges in 2025
Remote-controlled electric auger dredges enhance safety, reduce noise and emissions, improve efficiency, lower maintenance, and simplify transport for eco-friendly dredging in 2025.
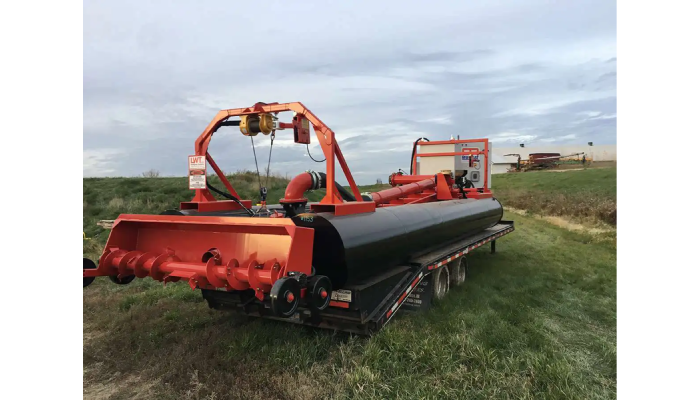
Using remote-controlled electric auger dredges in 2025 brings several practical benefits. First, operating equipment remotely keeps workers safe by letting them stay away from hazardous zones like deep waters or polluted sites. These dredges run on electric motors, cutting down noise and emissions, which helps meet stricter environmental rules while protecting aquatic life through precise sediment control. They also offer improved efficiency with consistent slurry handling and smart controls that adjust to site conditions automatically. Maintenance costs drop due to fewer mechanical parts and durable build quality, plus their modular design eases transport to remote locations. Altogether, these features make them a reliable and eco-friendly choice for various dredging tasks.
Enhanced Safety Through Remote Operation
Remote controlled dredge greatly improve operator safety by allowing control from as far as 1,000 feet away using reliable radio remote systems. This distance keeps workers out of harm’s way, especially in hazardous environments like contaminated sites, deep water, or areas with high levels of hydrogen sulfide gas. Features such as Auto Sense and Bottom Sense automate depth control, reducing the need for constant manual adjustments and lowering operator fatigue, which in turn decreases the chance of accidents during long shifts. Remote control units enable quick responses to changing conditions without requiring personnel near moving parts, minimizing risks of injury. Emergency stop functions can be activated instantly from a safe location, improving reaction times during dangerous situations. Furthermore, by reducing the number of workers on floating platforms, the risks of falls and drowning are significantly lowered. Maintenance tasks can also be scheduled with less human presence near heavy machinery, further protecting workers. Since operators remain onshore or in protected areas, remote operation supports safer dredging in adverse weather conditions. Overall, keeping personnel away from unstable, confined, or risky zones makes remote controlled dredging a safer choice for modern operations.
Superior Environmental Sustainability with Electric Auger Dredges
Electric auger dredges powered by electric motors play a crucial role in meeting the stricter environmental standards set for 2025 by eliminating diesel exhaust emissions. This shift drastically cuts greenhouse gases and reduces noise pollution, which benefits both local communities and wildlife. The use of anti-turbidity cutterheads minimizes sediment disturbance, preventing harmful plumes that can degrade water quality and harm aquatic ecosystems. These dredges also feature energy-efficient motors that consume less power, lowering the overall carbon footprint of dredging projects. Precise sediment removal techniques avoid unnecessary agitation of the water, helping to preserve aquatic habitats and maintain water clarity. Real-time remote monitoring and AI-assisted control systems allow operators to adjust dredging activities on the spot, protecting sensitive flora and fauna by optimizing dredging paths and reducing ecological impact. Additionally, electric systems have fewer risks of oil leaks or spills compared to diesel-powered machines, and their reduced vibration helps maintain the balance of underwater ecosystems. Many electric dredges can integrate with renewable energy sources, further enhancing their sustainability and aligning dredging operations with global green energy goals.
Operational Efficiency and Precision in Dredging
Remote controlled electric auger dredges in 2025 offer significant improvements in operational efficiency and precision. By creating uniform bottom profiles with parallel cuts, they prevent uneven surfaces that often lead to costly rework. Maintaining slurry solids concentration between 20-30% by volume optimizes dewatering and reduces material handling time, while variable frequency drives allow pump speeds to be fine-tuned for consistent slurry flow and enhanced productivity. Advanced GPS and AI guidance systems ensure dredging paths are followed with high accuracy, adjusting dynamically to changing sediment conditions to minimize wasted effort. Automated depth sensing removes guesswork, ensuring sediment is removed precisely without over-excavation, which saves time and fuel. Hydraulic direct drive pumps contribute to steady slurry delivery and improved reliability, reducing downtime caused by clogging or pump failures. Remote operation enables operators to quickly respond to site changes and maintain steady progress, supported by comprehensive data logging that aids performance analysis and future planning. Together, these features make remote controlled electric auger dredges a highly efficient and precise solution for modern dredging projects.
Cost-Effectiveness and Lower Maintenance Needs
Remote controlled electric auger dredges offer notable cost savings and reduced maintenance demands compared to traditional dredging equipment. Their simpler design includes fewer moving parts than cutter suction dredges, which means less frequent repairs and lower upkeep costs. Built with heavy-duty steel pontoons and strong frames, these dredges last longer and experience less downtime, maximizing operational time. Modular construction also makes transportation and assembly easier, cutting logistics expenses, especially for projects in remote locations. Automation reduces the need for large crews, lowering labor costs while speeding up project timelines. Technologies such as Pump Defender can cut downtime by up to 80% in debris-heavy waters by preventing suction loss. Electric drives consume less fuel and oil, further reducing operating expenses. The simplified electric systems require fewer specialized maintenance skills, and the limited number of hydraulic parts decreases leak risks and maintenance complexity. Lower noise levels mean fewer costly noise mitigation measures are necessary. Plus, remote diagnostics allow quick troubleshooting, minimizing repair time and improving overall equipment availability. Together, these factors make electric auger dredges a practical, economical choice for 2025 dredging needs.
Versatility Across Various Dredging Applications
Remote controlled electric auger dredges offer impressive versatility, making them suitable for a wide range of dredging projects. Whether working in reservoirs, ponds, wastewater treatment plants, mining tailings ponds, marinas, canals, or sensitive ecological zones, these dredges can adapt to the unique demands of each site. Their customizable dredging depths and ability to handle slurry densities tailored to project needs allow operators to efficiently manage sediment removal from soft silt to denser materials. Remote control capabilities make them especially useful in confined or hard-to-reach water bodies, where traditional equipment might struggle. Automation options such as Lateral Sense and Solids Sense enable precise adjustments for routine maintenance or more complex sediment challenges. The portable design supports quick redeployment across multiple locations, while electric power ensures compliance with strict emissions regulations, even in environmentally sensitive areas. Adjustable pumping distances and a low physical footprint allow these dredges to fit into diverse site layouts, including urban settings. Modular components further enhance scalability, letting operators handle everything from small ponds to large infrastructure projects with the same reliable equipment.
Technological Advances Shaping Future Dredging
Remote controlled electric auger dredges are becoming smarter and more efficient thanks to advances in automation and artificial intelligence. These machines are moving toward semi-autonomous or fully autonomous operation, reducing the need for constant human control and allowing for more precise dredging in challenging environments. AI-enhanced data analysis helps operators optimize resource use and improve productivity by adjusting dredging parameters in real time based on sediment conditions and site requirements. The integration of advanced sensors provides detailed feedback on sediment types and dredging conditions, enabling adaptive management that minimizes environmental impact. Additionally, wireless communication systems improve operational flexibility and safety by enabling remote diagnostics and predictive maintenance, which reduce downtime and equipment failures. Human-machine interfaces continue to evolve, making controls more intuitive and training quicker, which is crucial as dredging projects become more complex. Future electric dredges may also incorporate renewable energy sources, cutting carbon emissions further and aligning with growing sustainability goals. Machine learning algorithms are expected to play a bigger role by continuously analyzing performance data and fine-tuning operations for better efficiency and compliance with environmental regulations. These technological innovations collectively set the stage for a new era of dredging that is safer, greener, and more precise.
Improved Operator Experience and Training
Remote controlled electric auger dredges in 2025 offer a noticeably better operator experience through ergonomic design and advanced control systems. Cabins with climate control keep operators comfortable during long shifts, reducing fatigue and helping maintain focus. Intuitive fingertip controls simplify equipment handling and lower physical strain, making it easier to operate the dredge precisely. Industrial-grade remote units include clear error codes that allow quick troubleshooting, minimizing downtime and frustration. Training programs that come with the equipment ensure operators of all skill levels learn safe and effective operation, often supported by simulated modules that prepare users before they work in the field. Human-machine interface (HMI) systems provide easy-to-understand displays, speeding up learning curves and accommodating users with varied backgrounds. Remote controls also let operators work from safer, more comfortable locations away from the immediate dredging site, enhancing safety and convenience. Regular software updates improve control interfaces and add new features, while operator feedback systems help manufacturers refine controls and ergonomics over time. These improvements collectively reduce mistakes and increase productivity, making the dredging process smoother and safer for everyone involved.
Reduced Noise and Smaller Physical Footprint
Electric auger dredges powered by electric motors generate significantly less noise than traditional diesel engines, which helps minimize noise pollution near work sites. This quieter operation is especially beneficial in urban areas and wildlife habitats, where excessive noise can disrupt communities and sensitive ecosystems. The compact, containerized designs of these dredges improve maneuverability, allowing operators to work efficiently in tight or protected spaces without causing excessive disturbance. A smaller physical footprint means less disruption to shorelines and surrounding vegetation, while reduced vibration lowers the risk of damage to nearby structures and ecosystems. Because these dredges operate quietly, they can often run for extended hours without disturbing local residents or violating noise regulations. Additionally, their compact size enables access to previously unreachable or sensitive sites, expanding the range of projects that can be undertaken. Transport and setup are easier with these smaller units, reducing logistical challenges and lowering overall project costs. Finally, the reduced physical presence on the water helps minimize interference with other activities, making these dredges a practical choice for busy or environmentally sensitive locations.
Frequently Asked Questions
1. How do remote controlled electric auger dredges improve safety compared to traditional dredging equipment?
Remote controlled electric auger dredges reduce the need for operators to be physically close to the machinery, lowering the risk of accidents or exposure to hazardous environments. This remote operation helps keep workers safe from potential injuries and hazardous conditions often found around dredging sites.
2. In what ways do electric auger dredges offer environmental benefits over conventional dredging methods?
Electric auger dredges produce less noise and no direct emissions compared to diesel-powered equipment, resulting in reduced environmental impact. The precision of the auger also allows for more targeted sediment removal, which minimizes disruption to aquatic ecosystems and helps preserve water quality.
3. What makes remote controlled electric auger dredges more efficient in sediment removal tasks?
These dredges combine electric power with remote operation to optimize control and precision. They allow operators to adjust settings in real-time and quickly respond to varying sediment conditions, leading to faster and more consistent sediment extraction with less downtime.
4. How does the maintenance of remote controlled electric auger dredges compare to traditional dredging machines?
Electric auger dredges usually have fewer moving parts and don’t rely on complicated fuel systems, which reduces the frequency and complexity of maintenance. Additionally, remote monitoring features often enable early detection of issues, helping to prevent major breakdowns and extend the equipment’s lifespan.
5. What challenges might operators face when transitioning to remote controlled electric auger dredges?
Operators may need training to effectively manage the remote controls and understand the new technology. There could also be initial adjustments in workflow, as remote operation changes the way tasks are monitored and executed. However, these challenges typically lessen as users become more familiar with the system and its capabilities.
TL;DR Remote-controlled electric auger dredges in 2025 offer improved safety by keeping operators at a safe distance, while cutting emissions and noise with their electric power. They provide precise, efficient dredging with AI and GPS support, reduce maintenance costs, and adapt to various environments from reservoirs to sensitive habitats. Advanced automation and user-friendly controls simplify operation and training. Their compact design minimizes site impact, and proven projects show they deliver reliable, scalable performance for a range of dredging needs.

Lyle Vasquez is a technology blogger based in Connecticut. He has been passionate about technology since early childhood when he used to take apart and rebuild computers in his parent’s garage. Lyle’s tech-related blog posts are written to help others learn how to use the latest technology tools and devices. He loves to find new ways to integrate technology into everyday life. Lyle is a great resource for tech enthusiasts looking to stay up to date on the latest technologies.