Custom Injection Molding Solutions Enhance Product Life Cycle Management
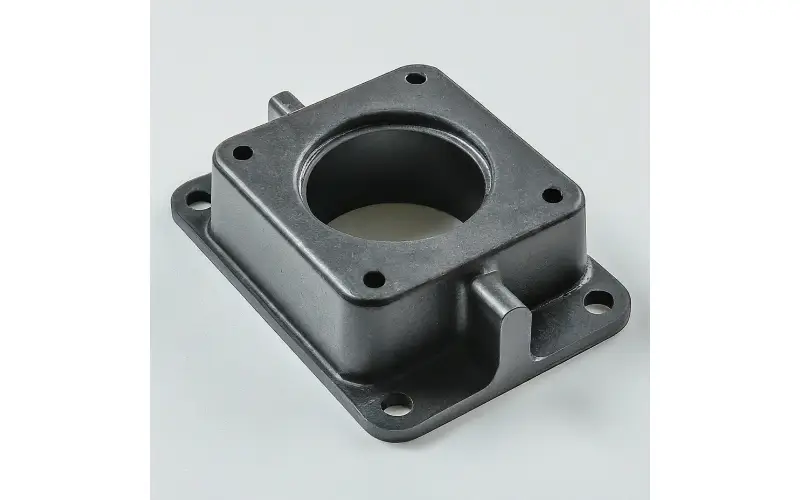
Custom injection molding solutions have become a cornerstone of modern manufacturing, offering precision, versatility, and cost efficiency across industries. These solutions play a critical role in enhancing product life cycle management by ensuring that every stage, from design to end-of-life, aligns with the highest quality standards. By tailoring components to specific requirements, businesses can achieve greater durability, sustainability, and innovation. As industries face evolving consumer demands and competitive markets, custom injection molding solutions are reshaping how products are conceptualized, produced, and optimized for long-term use.
How Custom Injection Molding Solutions Improve Product Durability?
Durability is a key factor in product success, influencing customer satisfaction and brand reputation. Custom injection molding solutions significantly enhance product durability by enabling the creation of components with superior structural integrity and resilience. Through advanced material selection, including reinforced polymers and composites, manufacturers can design parts that withstand environmental stresses, wear, and impact over time. Precise molding processes ensure uniformity, eliminating weak points that may compromise the product’s longevity. Additionally, the customization aspect allows engineers to optimize designs for specific use cases, reducing the likelihood of failure under real-world conditions. This durability not only extends the product life cycle but also minimizes maintenance costs and waste, contributing to sustainable practices.
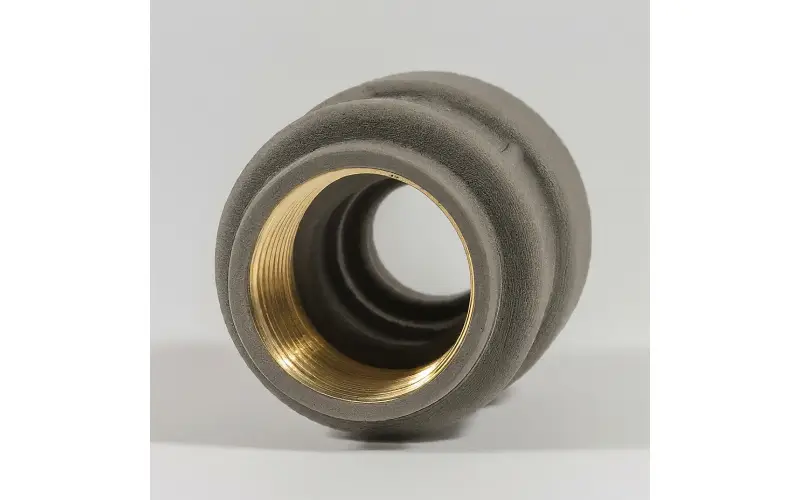
Benefits of Custom Injection Molding Solutions for Lifecycle Optimization
Custom injection molding solutions optimize every phase of the product life cycle, from prototyping to disposal. During the design phase, manufacturers can leverage injection molding to create detailed prototypes, reducing the time and cost associated with iterative development. In production, these solutions streamline the fabrication of complex parts with minimal material waste. Enhanced consistency and quality reduce the need for rework and recalls, leading to higher customer trust and retention. At the end of the product’s life, many injection-molded components can be recycled or repurposed, supporting circular economy initiatives. This lifecycle optimization not only reduces costs but also aligns with regulatory and environmental standards, ensuring long-term business viability.
Custom Injection Molding Solutions Ensure Superior Product Performance
Product performance is often determined by the precision and reliability of its components. Custom injection molding solutions excel in delivering parts that meet exact specifications, ensuring seamless integration and operation. By utilizing state-of-the-art machinery and mold designs, manufacturers can achieve exceptional dimensional accuracy, surface finish, and functionality. Customization enables the incorporation of features such as complex geometries, undercuts, and multi-material assemblies, which are difficult or impossible to produce using traditional methods. These innovations enhance the overall performance of the final product, giving businesses a competitive edge in the market. Furthermore, the ability to adapt materials and designs to specific industry standards ensures that products consistently exceed customer expectations.
Streamlining Production with Custom Injection Molding Solutions
Efficient production processes are essential for meeting market demands and reducing costs. Custom injection molding solutions streamline manufacturing by automating the creation of high-quality components at scale. Advanced molding techniques, such as overmolding and insert molding, allow for the integration of multiple functions into a single part, reducing assembly time and complexity. The repeatability of injection molding ensures consistent output, even for high-volume production runs. Additionally, the use of computer-aided design (CAD) and simulation tools during the mold design phase minimizes errors and accelerates production timelines. This streamlined approach not only enhances productivity but also enables faster response to market trends and customer needs.
Custom Injection Molding Solutions Support Sustainable Product Design
Sustainability is a growing priority for manufacturers, and custom injection molding solutions offer several pathways to eco-friendly production. By optimizing material usage, these solutions reduce waste during the molding process. Many injection-molded components can be made from biodegradable or recycled materials, further minimizing environmental impact. Customization enables the design of lightweight yet durable parts, reducing resource consumption and energy use in downstream applications. Additionally, the precision of injection molding minimizes the need for secondary machining or processing, saving energy and raw materials. By incorporating sustainable practices at every stage, manufacturers can align with environmental regulations and meet the expectations of environmentally conscious consumers.
Enhancing Efficiency with Custom Injection Molding Solutions in Manufacturing
Efficiency in manufacturing is critical for maintaining profitability and competitiveness. Custom injection molding solutions enhance efficiency by reducing production times, material waste, and labor costs. Automation and robotics play a significant role in modern injection molding, enabling faster cycle times and consistent quality. The ability to produce intricate and multi-functional parts in a single operation reduces the need for post-processing and assembly, further improving operational efficiency. Additionally, the use of predictive maintenance and real-time monitoring systems ensures that injection molding machines operate at peak performance, minimizing downtime and disruptions. This increased efficiency not only supports higher output but also reduces overall manufacturing costs.
Custom Injection Molding Solutions Drive Innovation in Product Lifecycle Management
Innovation is at the heart of product development, and custom injection molding solutions are a catalyst for creative design and advanced manufacturing techniques. By offering unparalleled flexibility in material selection and part design, injection molding enables the creation of products that push the boundaries of functionality and aesthetics. Innovations such as multi-material molding, 3D-printed molds, and micro-molding open new possibilities for industries ranging from medical devices to consumer electronics. These advancements not only enhance the product life cycle but also enable businesses to differentiate themselves in crowded markets. By integrating custom injection molding into their operations, companies can stay ahead of industry trends and continually deliver cutting-edge solutions to their customers.
Conclusion
Custom injection molding solutions are revolutionizing product life cycle management by enhancing durability, optimizing processes, and fostering innovation. From reducing waste and improving sustainability to delivering superior performance and efficiency, these solutions address the diverse needs of modern manufacturers. As industries continue to evolve, the ability to customize and refine injection molding processes will remain a vital asset in creating products that are durable, sustainable, and competitive. By embracing the potential of custom injection molding solutions, businesses can achieve long-term success and contribute to a more sustainable future.

Jon Burton, a dedicated advocate for education reform, navigates the landscape of learning with passion and purpose. With a profound belief in the transformative power of education, Jon explores innovative approaches to teaching and learning, seeking to inspire and empower students of all ages. Through his writings, he shares insights into educational theory, curriculum development, and classroom practice, aiming to foster a culture of lifelong learning and intellectual curiosity.